Raising the roof
A dedicated department for all seasons
At Industriepark Höchst, Claus Fischer is the lord of the roofs. His kingdom covers an entire square kilometer of roof surface – spread among 800 buildings. Fischer is responsible for their maintenance as a specialist designer.
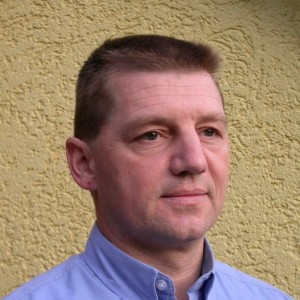
I’ve been on every single roof in this park. And we have a wide variety of roof types for a wide variety of requirements.
Claus Fischer, Infraserv Höchst / Facilities Services, Master Roofer
When you have a million square meters to oversee, you always have a construction site somewhere – from historic Wilhelminian-era office buildings to newly built structures with green roofs. A roof lasts 30 years on average, but that is just a statistic. After all, a roof has to meet much more demanding requirements than just keeping out the snow and rain.
Such as keeping in the heat: Buildings lose most of their energy through the roof. That explains the current popularity of energy-efficient roof retrofits – which have both environmental and economic motivations. Besides installing modern insulation, a cutting-edge heat recovery system can lower operating costs dramatically. And that holds true even though the park’s dedicated power station has made electricity so cheap that few building owners are even considering photovoltaic systems.
Every roof restoration begins with an initial assessment, which is billed based on a separate preliminary design quotation. “After all, we can’t quote a real price until we know the actual condition of the roof,” said Fischer. The assessment includes an extensive consultation in which the parties work out a compromise between what the customers want and what the roof experts believe the customers need.
Contamination is an important issue. Around 80% of roofs built in the 1960s are contaminated. Luckily, Infraserv Höchst has in-house toxic substance laboratories that can promptly analyze samples and measure contamination.
- Roofs often contain asbestos and carcinogenic PAHs.
- Cork insulation also gives off gases from binders such as phenol resin; older cork panels use bitumen as a binder, which requires special handling during its removal and disposal.
- When older roofs are repeatedly repaired, the non-repaired sections are often difficult to remove as well.
- 9 mm of bitumen will seal a roof adequately. It is also a reasonably thick layer that can easily be cut up into transportable pieces with a carpet knife. However, the layers on some roofs can be up to 80 mm thick – and so have to be removed with a machine.
Surprises galore hide underneath the roof covering. Depending on what is being made in the building, the production emissions may corrode certain materials more than others. In many modern industrial buildings, the roof coverings rest on steel or aluminum frames. However, it may still be appropriate to build a brand-new frame out of timber. This is where our designers draw on their expertise and experience and carefully assess what chemical processes will be unfolding under the roof.
Industrial buildings present special challenges in leak prevention. Countless ducts and pipes pass through the roof. Not to mention basic fire protection devices such as smoke vents. However, to a roofer, every penetration in the roof is a weak point that can let in moisture. To minimize these weak points, it is recommended to install an enclosed mechanical penthouse on the roof, especially for laboratory buildings with cleanrooms and other sensitive room-in-room structures. It also simplifies maintenance – technicians do not have to clamber around on slick wet roofs to service the equipment.
Safety is Infraserv’s top priority
Speaking of clambering around, safety is incredibly important. Whereas roofers used to regularly climb up and down roofs – which were all equipped with evenly spaced anchor points – railings are now mounted around the entire roof perimeter during construction. They even surround skylights to prevent people from falling into the building as well. Unlike ordinary residential buildings, industrial roofs are not solely the province of framing carpenters, roofers and chimneysweeps, who routinely work at heights. Electricians, HVAC technicians and other “civilians” have to get out onto the roof, too. Of course, if Fischer had his way, every roof would automatically be equipped with permanent railings. But the local historical preservation commission does not always agree.
It should be noted that all roofs, even flat ones, should be sloped across their entire surface so that water can drain off. Large surfaces tend to sag over time – a sign of aging that may not be immediately visible to the naked eye. Sagging is particularly common among roofs that are carrying their maximum design load or have a particularly long span. It often remains hidden until rainfall accumulates and fails to drain off, leaving behind a puddle on the roof. The solution: 3D CAD scans can take detailed measurements of roof deflection. They also make the process of designing a new roof much easier and more reliable since they visualize all the structures and drainage pathways from all directions in advance.
For Fischer, it’s only natural to do all the restoration work while the production process continues underfoot, even under clean room conditions. After all, extreme flexibility is a core trait for all Infraserv Höchst service departments. As a general contractor, Infraserv handles inspection, assessment, consulting and construction site management – all from a single source. That is why it has been fielding a growing number of inquiries from outside the industrial park, too.